Blowout Preventer (BOP): A Critical Safety Device in Oil and Gas Drilling
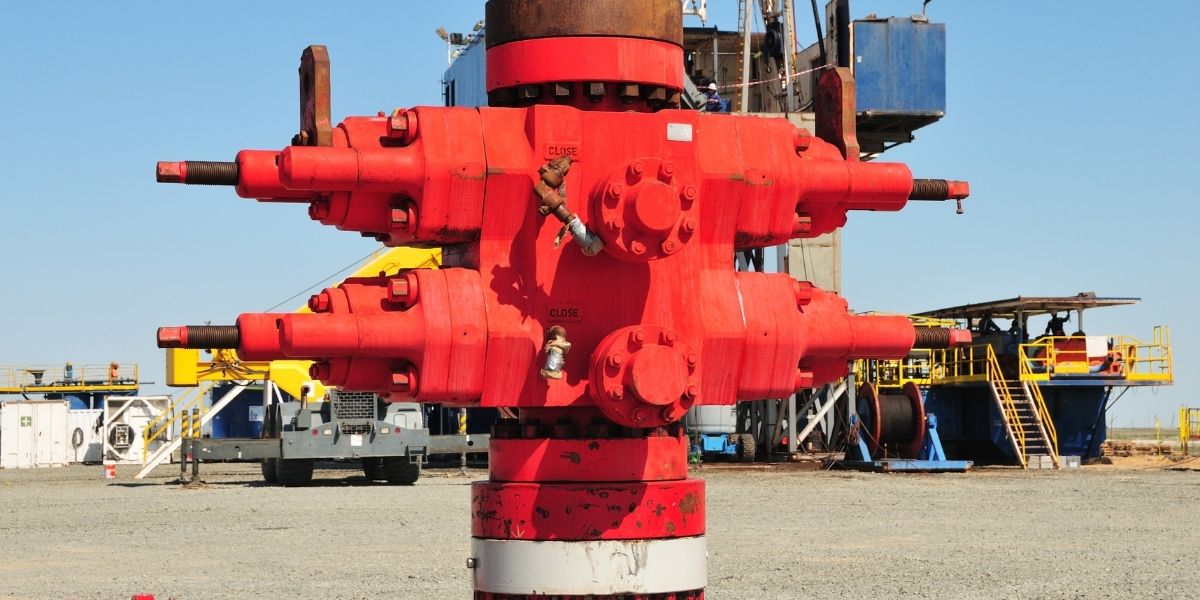
In the oil and gas industry, safety is paramount, and one of the most critical pieces of equipment designed to prevent catastrophic accidents is the blowout preventer (BOP). A blowout preventer is a specialized device used to seal, control, and monitor oil and gas wells, especially during drilling operations. The primary function of a BOP is to prevent blowouts—uncontrolled releases of oil, gas, or other well fluids—by safely containing the high-pressure formations encountered during drilling.
Blowouts can have devastating consequences, including loss of life, environmental damage, and the destruction of valuable assets. The BOP system serves as a vital safeguard in protecting the well and the surrounding environment, making it a key element in the drilling process. This article will delve into the history, functions, types, components, and importance of blowout preventers, as well as their role in preventing disasters like the 2010 Deepwater Horizon incident.
The Role and Function of a Blowout Preventer
A blowout preventer is essentially the last line of defense in controlling well pressure. When drilling into the Earth’s subsurface, oil and gas operators frequently encounter high-pressure reservoirs. These pressure changes can sometimes be unpredictable, and if they exceed the capacity of the wellbore, they can cause a blowout. A blowout is a dangerous, high-pressure event where the well fluids, including hydrocarbons, are ejected uncontrollably to the surface.
The BOP is installed at the top of the wellhead during drilling and is designed to either seal the well completely or to divert the flow of fluids safely away from the drilling site. If well control is lost, the BOP system can be activated to shut in the well and control the situation, preventing the uncontrolled flow of fluids to the surface.
Primary Functions of a Blowout Preventer
Pressure Control: The BOP system is designed to contain and control wellbore pressure, ensuring that pressure spikes do not result in a blowout. It allows for the safe management of any pressure surges encountered during drilling operations.
Shutting In the Well: One of the main functions of a BOP is to completely seal the well, stopping the flow of oil, gas, or other fluids. This can be necessary if an unexpected pressure surge occurs or if the well needs to be shut down for safety reasons.
Well Monitoring: BOPs are equipped with pressure sensors and gauges that allow operators to monitor wellbore conditions in real-time. These monitoring systems provide critical data that helps in decision-making during drilling operations.
Diverting Flow: In cases where the well cannot be sealed completely, the BOP can divert fluids away from the wellhead to prevent hazardous conditions on the rig. The diverted fluids are directed to a safer area where they can be controlled and processed.
Providing Access for Well Control Operations: The BOP also facilitates the introduction of kill fluids into the wellbore to balance pressure and regain control of the well during critical situations. It enables the use of specialized tools and methods to bring the well back to a controlled state.
Blowout Preventer in Action: Case of Deepwater Horizon
The Deepwater Horizon disaster in 2010 is a stark reminder of the importance of BOPs and the risks associated with their failure. In this case, the BOP failed to properly seal the well after a blowout, resulting in the uncontrolled release of oil and gas from the Macondo well in the Gulf of Mexico. The failure of the BOP system contributed to the largest marine oil spill in history, with devastating environmental and economic impacts.
The incident highlighted the need for more stringent testing, maintenance, and operational protocols for BOPs, as well as the importance of robust design and redundant safety features to ensure that the device functions correctly in emergency situations.
History of the Blowout Preventer
The concept of a blowout preventer was first developed in the early 20th century as oil and gas drilling became more complex and wells reached deeper, higher-pressure formations. Before the development of BOPs, blowouts were common and often resulted in catastrophic loss of life and property.
The first blowout preventer was invented by James S. Abercrombie and Harry S. Cameron in 1922. Known as the “ram-type” blowout preventer, their device featured sliding rams that could close off the wellbore in the event of a blowout. This early BOP was a breakthrough in well control technology and laid the foundation for modern BOP designs.
As oil and gas exploration moved offshore and into deeper, more challenging environments, blowout preventer technology continued to evolve. Today’s BOPs are highly sophisticated systems that incorporate multiple layers of redundancy and advanced monitoring capabilities, making them critical to safe drilling operations both onshore and offshore.
Types of Blowout Preventers
Blowout preventers can be broadly categorized into two main types: ram-type blowout preventers and annular blowout preventers. Both types serve the same purpose of sealing the wellbore, but they operate using different mechanisms and are often used in conjunction to provide a comprehensive well control system.
1. Ram-Type Blowout Preventers
The ram-type blowout preventer is one of the most common and historically significant types of BOP. It uses steel rams, which are large, piston-like components that slide across the wellbore to seal it off. Ram BOPs come in several different configurations, each designed for specific well control scenarios.
Types of Rams
Pipe Rams: Pipe rams are designed to seal around the drill pipe. They feature semicircular cutouts that match the size of the pipe, allowing them to close around the pipe without damaging it. Pipe rams are used when the well is being drilled and the drill string is in place.
Blind Rams: Blind rams are used to completely seal the wellbore when there is no pipe in the hole. These rams close off the well entirely, blocking any fluid or gas from escaping. Blind rams are typically used when the well needs to be shut in during an emergency or after the drilling pipe has been removed.
Shear Rams: Shear rams are designed to not only close the wellbore but also cut through the drill pipe if necessary. In extreme cases where well control is lost and other methods of sealing the well have failed, shear rams can be activated to shear through the drill pipe and completely seal the well. This function is considered a last-resort safety measure.
Variable Bore Rams: These are a more advanced type of ram that can accommodate pipes of varying diameters. This versatility makes them useful in situations where the drill string changes size as the well progresses.
2. Annular Blowout Preventers
Annular blowout preventers, also known as “bag-type” BOPs, operate using a flexible rubber element called a packing unit, which is capable of sealing the wellbore by expanding and contracting around the drill pipe or casing. The annular BOP can seal off the wellbore around a wide range of pipe sizes, making it a more versatile option compared to ram BOPs.
The annular BOP is often used as the first line of defense in well control operations because of its ability to seal around irregularly shaped objects or even open holes. It is typically placed above the ram-type BOPs in a BOP stack, providing an additional layer of security.
Advantages of Annular BOPs
Versatility: Annular BOPs can seal around various sizes of drill pipe, casing, or even open holes, making them a flexible solution in well control situations.
Pressure Management: These BOPs are ideal for managing wellbore pressure during drilling operations because they can maintain a controlled seal even as the drill string moves up and down through the wellbore.
Safety: Annular BOPs are often used in combination with ram-type BOPs to create a fail-safe system. If the annular BOP cannot control the well pressure, the ram BOPs provide a second line of defense.
BOP Stack: Combining Multiple BOPs for Maximum Safety
In practice, blowout preventers are not used in isolation. Instead, they are typically arranged in a BOP stack, which consists of multiple BOPs (both ram-type and annular) installed on top of one another. This configuration provides redundancy, ensuring that if one BOP fails, another can be activated to control the well.
A typical BOP stack might include:
An annular BOP at the top of the stack
Pipe rams for sealing around the drill pipe
Blind rams for sealing the well when no pipe is present
Shear rams for emergency situations where the drill pipe must be cut
The stack is usually mounted on top of the wellhead and is designed to be easily accessible and operable in the event of an emergency. In offshore drilling, particularly in deepwater operations, the BOP stack is often located on the seabed, where it can be remotely operated from the surface.
Components of a Blowout Preventer System
The blowout preventer is part of a larger system that includes various components designed to ensure safe drilling operations. These components work together to monitor, control, and manage well pressure.
1. Accumulator Units
An accumulator unit is a key part of the BOP control system. It stores hydraulic fluid under pressure, which is used to operate the BOP’s rams and valves. The accumulator provides the hydraulic power needed to close the BOP in the event of an emergency.
2. Control Panels
The BOP is controlled using a series of control panels, which can be located on the drilling rig or remotely for subsea operations. These panels allow operators to activate or deactivate the BOP, monitor well pressure, and perform routine tests on the system.
3. Choke and Kill Lines
Choke and kill lines are pipelines connected to the BOP system that allow for the circulation of fluids in and out of the wellbore. Choke lines are used to control the flow of fluids from the well, while kill lines are used to pump heavy fluids (kill fluid) into the well to regain pressure control.
4. Remote Operated Vehicles (ROVs)
In subsea drilling, ROVs are used to operate and maintain BOPs located on the seabed. These unmanned underwater vehicles can perform tasks such as valve manipulation, visual inspection, and emergency operations when human intervention is not possible.
Maintenance and Testing of Blowout Preventers
Given their critical role in well control, blowout preventers are subject to rigorous maintenance and testing protocols. Regular inspections are essential to ensure that the BOP is functioning correctly and will operate as intended in an emergency.
Routine Testing
BOPs undergo routine pressure tests to verify their integrity and functionality. These tests involve applying pressure to the BOP and observing its ability to seal the wellbore. Any leaks or malfunctions must be addressed immediately to ensure the safety of the well.
Certification and Compliance
Blowout preventers are subject to strict regulatory standards set by organizations such as the American Petroleum Institute (API) and various governmental agencies. These standards specify the design, testing, and maintenance requirements for BOP systems to ensure they meet the necessary safety and performance criteria.
The Future of Blowout Preventer Technology
As oil and gas exploration moves into deeper and more complex environments, the demands placed on blowout preventers continue to increase. Advancements in BOP technology are focused on improving reliability, automation, and remote monitoring capabilities.
1. Automated BOP Systems
One of the key trends in BOP technology is the development of automated systems that can monitor well conditions in real-time and automatically activate the BOP if pressure anomalies are detected. These systems reduce the reliance on human intervention and improve response times in emergency situations.
2. Remote Monitoring and Control
In deepwater drilling, where BOPs are located thousands of feet below the surface, remote monitoring and control systems are essential. New technologies are being developed that allow operators to control BOP systems from onshore facilities, reducing the need for offshore personnel and improving safety.
3. Enhanced Shear Ram Capabilities
Recent advancements in shear ram technology have focused on improving their ability to cut through larger, stronger drill pipes and other wellbore components. These enhanced shear rams provide a more reliable last-resort option for sealing the well in emergency situations.
Conclusion
The blowout preventer is a critical blowout preventer device in the oil and gas industry, designed to prevent blowouts and protect lives, assets, and the environment. Its development over the past century has significantly reduced the frequency of blowouts, but as incidents like the Deepwater Horizon disaster show, the need for continual improvement in BOP technology and practices is paramount.
As drilling operations move into more challenging environments, the role of the BOP will only grow in importance. Through rigorous testing, maintenance, and technological innovation, the industry continues to enhance the safety and reliability of blowout preventers, ensuring that they remain an essential tool in the prevention of oil and gas well blowouts.