Why is Regular Monitoring of Industrial Lubricants Essential?
Why is Regular Monitoring of Industrial Lubricants Essential?
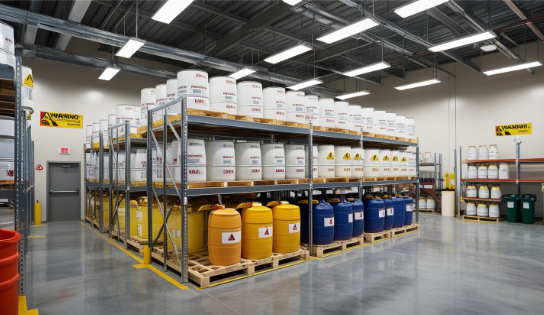
Industrial lubricants play a critical role in maintaining the performance and longevity of machinery in various industries. Whether used in manufacturing, mining, or any other sector relying on mechanical systems, lubricants ensure smooth operation by reducing friction, dissipating heat, and preventing corrosion. However, to ensure these lubricants continue to perform at optimal levels, it is essential to monitor their condition regularly. Regular monitoring helps detect issues before they lead to equipment failure, enhances operational efficiency, and contributes to cost savings.
This article explores the reasons why regular monitoring of industrial lubricants is crucial, particularly for businesses like Northern Metalic, which is a leading supplier of lubricants in Canada. The importance of maintaining high-quality lubricants cannot be overstated, especially when considering the significant impact they have on machinery uptime and overall productivity.
1. Preventing Equipment Failure
One of the primary reasons for monitoring industrial lubricants is to prevent unexpected equipment failure. Lubricants play a critical role in reducing friction between moving parts, and if the lubrication is insufficient or contaminated, the machinery can suffer from increased wear and tear. Regular monitoring helps to identify signs of lubricant degradation, contamination, or insufficient viscosity, which could indicate a risk of failure.
By routinely checking the lubricant’s condition, operators can detect problems such as excessive heat buildup or particles within the fluid, which could cause damage to vital components. Early detection allows maintenance teams to take corrective actions before major damage occurs, reducing the risk of downtime and expensive repairs.
2. Ensuring Optimal Lubricant Performance
Lubricant properties can change over time due to exposure to heat, pressure, and contaminants. For instance, industrial lubricants can become oxidized, lose viscosity, or become contaminated with dirt, moisture, or metal particles. These changes can significantly impact the lubricant’s ability to perform its role efficiently. Regular monitoring enables businesses to assess the effectiveness of their lubricants and make adjustments as necessary to ensure optimal performance.
Through routine tests, such as viscosity checks, particle counting, and spectrometric analysis, companies can determine if their lubricants are still suitable for use. If the tests show that the lubricant is no longer performing as expected, operators can decide to replace or treat the lubricant, ensuring that equipment continues to run smoothly and efficiently.
3. Reducing Maintenance Costs
Lubricant monitoring can lead to significant cost savings by extending the life of machinery and reducing the frequency of breakdowns. Proactive monitoring of industrial lubricants helps identify issues before they result in costly equipment damage or unplanned maintenance. For instance, detecting contamination or degradation in the lubricant early on can prevent the need for expensive repairs, replacements, or even complete system overhauls.
Furthermore, by adjusting lubrication schedules based on the actual condition of the lubricant, businesses can avoid unnecessary lubricant changes, optimizing costs while ensuring that machinery is always well-lubricated. Regular monitoring ensures that lubricants are replaced only when necessary, saving both on the lubricant itself and on the labor costs associated with frequent maintenance.
4. Improving Energy Efficiency
Worn-out or contaminated lubricants can lead to increased friction and heat, which forces machinery to work harder to perform at the same level. This additional strain results in higher energy consumption and reduced overall efficiency. By monitoring the condition of industrial lubricants, businesses can ensure that machinery operates at peak efficiency, reducing energy costs and contributing to more sustainable operations.
Optimized lubricant use not only improves the energy efficiency of the machinery but also reduces the overall environmental impact. By preventing excessive energy consumption, businesses can reduce their carbon footprint while also decreasing their operating expenses.
5. Extending Equipment Lifespan
Lubricants serve as a protective barrier, preventing direct contact between metal surfaces and reducing wear and tear. By monitoring the condition of lubricants, businesses can ensure that their machinery receives continuous protection from corrosion, oxidation, and abrasive wear. This proactive approach can help extend the life of equipment, which is particularly valuable for industries with high-value machinery that can be expensive to replace.
Furthermore, monitoring ensures that lubricants continue to offer the appropriate protection for the type of machinery being used, which is crucial for industries relying on specialized equipment with high precision and performance requirements.
6. Ensuring Compliance with Industry Standards
Many industries are subject to strict regulations regarding environmental impact, safety, and quality control. Monitoring industrial lubricants helps ensure that businesses comply with these regulations by ensuring that lubricants are not contaminated or harmful to the environment. For example, some industries have guidelines for managing waste lubricants and ensuring that they are disposed of properly.
Regular monitoring ensures that businesses meet industry standards for lubricant quality, helping them avoid fines, legal issues, or damage to their reputation. It also ensures that companies adhere to best practices for lubricant management, which can improve relationships with regulators, customers, and other stakeholders.
7. Data-Driven Decision Making
Regular lubricant monitoring provides valuable data that can help businesses make informed decisions about their equipment and maintenance schedules. By keeping track of lubricant performance over time, businesses can spot trends and make predictions about when maintenance will be needed or when equipment might start to show signs of wear.
This data-driven approach allows businesses to plan maintenance more effectively, optimize their operations, and avoid unanticipated downtime. Additionally, operators can tailor their maintenance strategies to the specific needs of the machinery and its operating conditions, improving the overall reliability of the equipment.
8. Reducing Downtime and Improving Productivity
One of the most costly aspects of industrial operations is unplanned downtime. Regular lubricant monitoring helps businesses avoid the disruptive effects of unscheduled equipment failure by identifying potential issues early. This proactive approach reduces the likelihood of breakdowns and allows maintenance to be performed at more convenient times.
By preventing unexpected failures and extending the life of machinery, companies can ensure that their production processes run smoothly and without interruptions. This contributes to higher productivity, better utilization of resources, and an overall improvement in operational efficiency.
9. Industrial Lubricants Clairmont: The Role of Local Suppliers
For businesses operating in the Clairmont area, it’s essential to partner with reliable lubricant suppliers like Northern Metalic. Industrial lubricants Clairmont play an important role in maintaining the health of machinery, and choosing the right supplier can make a significant difference in operational performance. Northern Metalic offers top-quality lubricants and maintenance solutions that are tailored to the specific needs of the region’s industrial sector. For more information.
10. Conclusion
In conclusion, regular monitoring of industrial lubricants is essential for ensuring optimal performance, reducing maintenance costs, extending equipment lifespan, and improving overall productivity. By keeping track of lubricant condition, businesses can identify potential issues early, avoid costly repairs, and enhance operational efficiency. For companies like Northern Metalic, offering high-quality lubricants, regular monitoring is a crucial component of ensuring that their customers’ machinery runs smoothly and remains in excellent condition. Emphasizing the importance of routine lubricant checks can significantly contribute to the long-term success of industrial operations, ensuring equipment performs reliably and efficiently for years to come.